Wir freuen uns, Sie auf unserem Blog begrüßen zu dürfen. Hier finden Sie Wissenswertes, Anwendungen und Hilfestellungen rund um die Themen Automatisierung, industrielle Sensorik und Explosionsschutz.
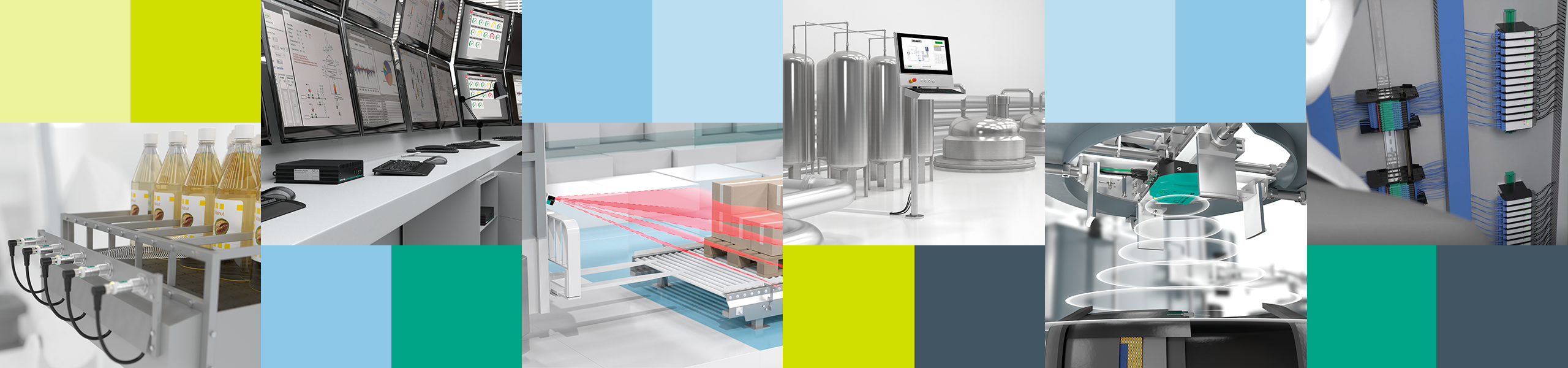
Willkommen auf unserem Blog. Hier finden Sie aktuelle Beiträge rund um die Themen Automatisierung und Sensorik.
Sichere Füllstandsmessung – Warum zwei verschiedene Technologien entscheidend sind
Füllstandsmesstechnik ist die Grundlage für eine zuverlässige Prozesssteuerung in chemischen, petrochemischen, umwelt- und prozesstechnischen Anwendungen. Erfahren Sie, warum es bei kritischen Tankfüllstandsmessungen ratsam ist, zwei verschiedene Technologien für die kontinuierliche Füllstandsmessung und die Grenzwerterfassung zu verwenden.
Häufig gestellte Fragen zu Reflexionslichtschranken und Reflektoren
Wir beantworten die am häufigsten gestellten Fragen über den Einsatz von Reflexionslichtschranken und welche Art von Reflektor für Ihre Anwendung geeignet ist.
Vier TCP-basierte Kommunikationsprotokolle als Schlüssel für das IIoT – Teil 3: AMQP
Erfahren Sie mehr über die wichtigsten Merkmale des interoperablen asynchronen Publish/Subscribe-Kommunikationsprotokolls AMQP. Wir werfen einen genaueren Blick auf die Interoperabilität, das Echtzeitverhalten, die Sicherheit, die Implementierung und die typischen Anwendungen von AMQP im Vergleich zu MQTT.
Eigensicheres Smartphone Smart-Ex® 03 mit Allround-Schnittstelle USB-C
Das eigensichere, 5G-fähige Android-Smartphone Smart-Ex 03 verfügt über die Standardschnittstelle USB 3.1 Typ-C und bietet Ihnen über einen Multiport-Adapter ein komplettes Desktop-Erlebnis. Erfahren Sie mehr über die Vorteile, die der USB-C-Anschluss für Ihre digitalen Anwendungen bietet.
Vier TCP-basierte Kommunikationsprotokolle als Schlüssel für das IIoT – Teil 2: OPC UA
TCP-basierte Kommunikationsprotokolle ermöglichen die smarte Kommunikation bis in die Cloud. Erfahren Sie mehr über die Interoperabilität, das Echtzeitverhalten, die Sicherheit, Implementierung und Anwendungen von OPC UA.
Vier TCP-basierte Kommunikationsprotokolle als Schlüssel für das IIoT – Teil 1: MQTT
Was ist MQTT und wie funktioniert es? Erfahren Sie alles über die Interoperabilität, das Echtzeitverhalten, die Sicherheit sowie die Implementierung und Anwendung von MQTT.
Abonnieren Sie unseren Newsletter und erhalten Sie regelmäßig Neuigkeiten und Wissenswertes aus der Welt der Automatisierung.